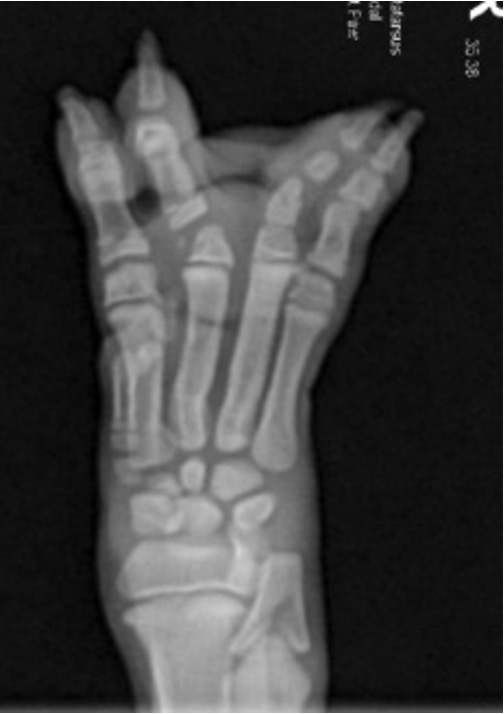
The main goal of this project was to determine if additive manufacturing can be used to
develop a custom brace prototype which would be more affordable compared to other braces on
the market right now.
One main goal was to create a brace that would immobilize the phalanges metacarpus at 90
degrees for optimal
recovery. This brace will also try to restrict the carpal joint range of motion while also
supporting the paw and distributing the load. The first model was based off some generic
braces and custom braces on the market with similar goals. an open sleeve is incorporated
for the arm and a paw cup is added to support the paw. In the second iteration, a hinge was
added for the carpal joint but the paw cup and metacarpal were kept as one piece to maintain
a 90 degree angle even during walking to optimize healing.
An AM assessment was performed to determine if this method was the best method for producing
this product, some
trade offs would be material selection. We wanted to choose something that would be
compatible with soft tissue, would also be light weight, and would be hard enough to
withstand the forces when in use. With the timeline and budget of this project as well as
considering what materials would be compatible with additive manufacturing, getting these
characteristics in one material would have been very expensive so we decided to go with PLA
as it is easy to iterate, quick to print, and affordable.
Because the brace is fully customizable, that comes at a price when manufacturing these
products. Because we decided to use additive manufacturing processes, the customization
price point is lower than if we used more traditional methods which also ties in to the
point that additive manufacturing is more cost effective in more complex parts.
PLA is easy to print which parallels well with our short timeline as
we were able to complete multiple iterations with little waste and a small economic burden.
Because the prototypes were cheap and simple, it did prolong our developmental phase and
ultimately did not allow us to use our final material PCL which is a common biocompatible
material as well as flexible which would provide comfort while still providing support.