Hydroponic Greenhouse
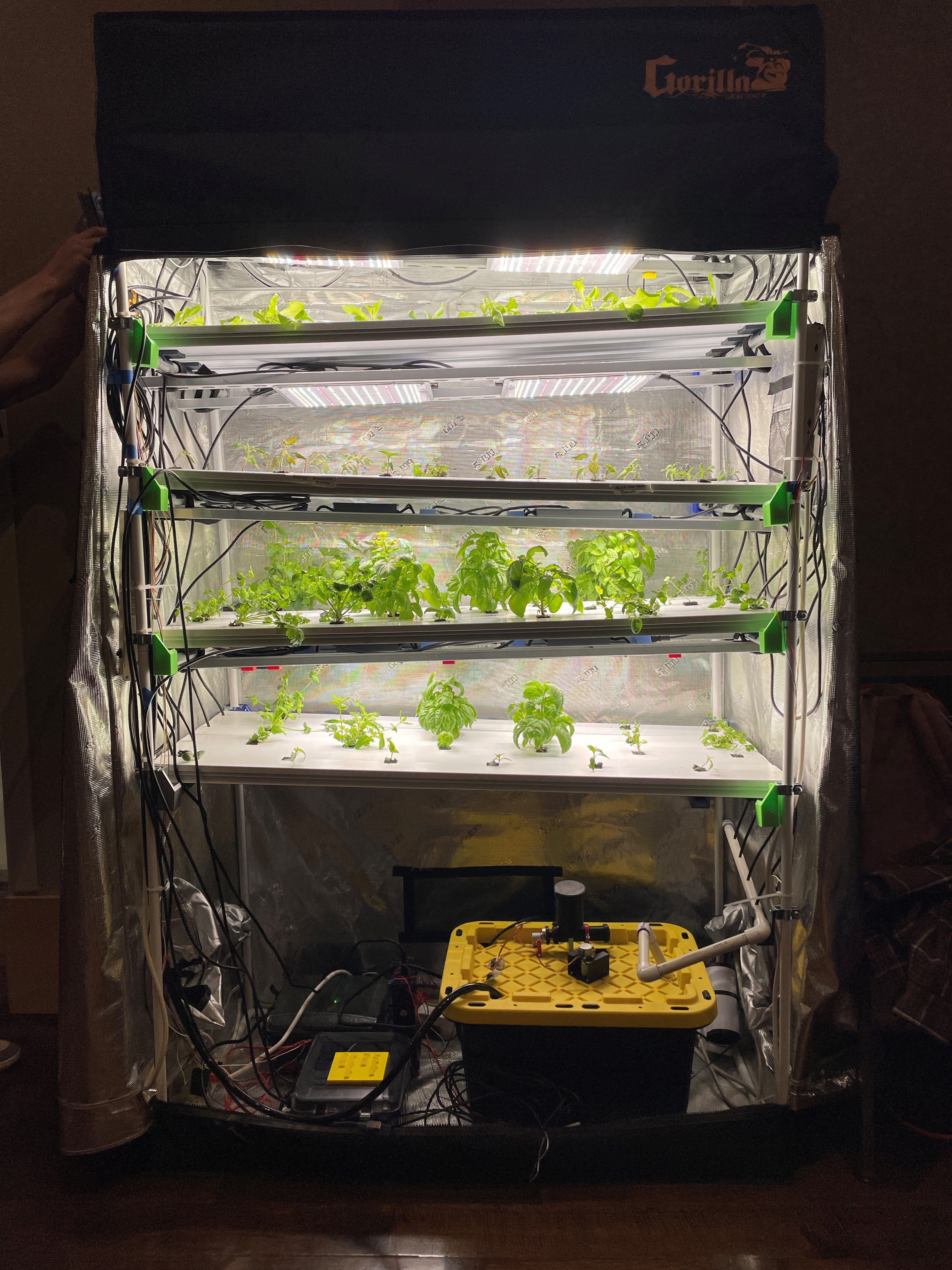
Senior Design Capstone Project:
A year long project producing a dully autonomous
hydroponic greenhouse from scratch.
Senior Design Capstone Project:
A year long project producing a dully autonomous
hydroponic greenhouse from scratch.
A project exploring additive manufacturing practices and their applications in custom products compared to traditional methods of manufacturing.
The main goal of this project was to develop mechatronics skills and introduce students to developing original Arduino code using Arduino libraries and parts. This project developed Arduino code to autonomize a rotating food plate and a 4 bar linkage attached to a knife which would act as a modified food processor to slice food. This project produced a working prototype using Arduino motors, LEDs, an ultrasonic sensor, piezo speaker, buttons, and housings modeled in SolidWorks and prototyped with 3D printed materials.
The main goal of this project was to introduce machines and machine shop protocols to undergraduates. This clock utilized four materials and a wide range of machines to create a fully working product. The aluminum base utilitzed milling and the CNC machine to create text on the base. The brass and steel pieces were cut, then turned to size using the lathe tips ground by students, then drilled or tapped on a lathe for attachment to the aluminum base. The clock face is made from PMMA which was cut then filed down to the correct shape. These specifications derived from engineering drawings then checked against GD&T specifications.
The main goal of this project was to utilize the drop forge and manual lathe. For this project, students were given a casted piece of aluminum with a screwdriver shank. The manual lathe was used to drill pilot holes then knurled with the knurling attachment to give it the diamond pattern. Then to achieve a flat head for the screwdriver, the shank was heated up, then the drop forge was used to mold the head shape, throughout the process, the shank was quenched in oil and water then ground to a polished finish. These specifications derived from engineering drawings then checked against GD&T specifications.
This project aimed to introduce students to G Code and CNC machines. This project started with a 5"X5" aluminum piece. An individual CAD file was designed by students then converted to G Code for the CNC machine. I chose to utilize sand blasting to achieve a frosted look on the trivet. After blasting, the trivet was cut using the CNC machine allowing for a contrasting shiny design against the matte sand blasted finish.